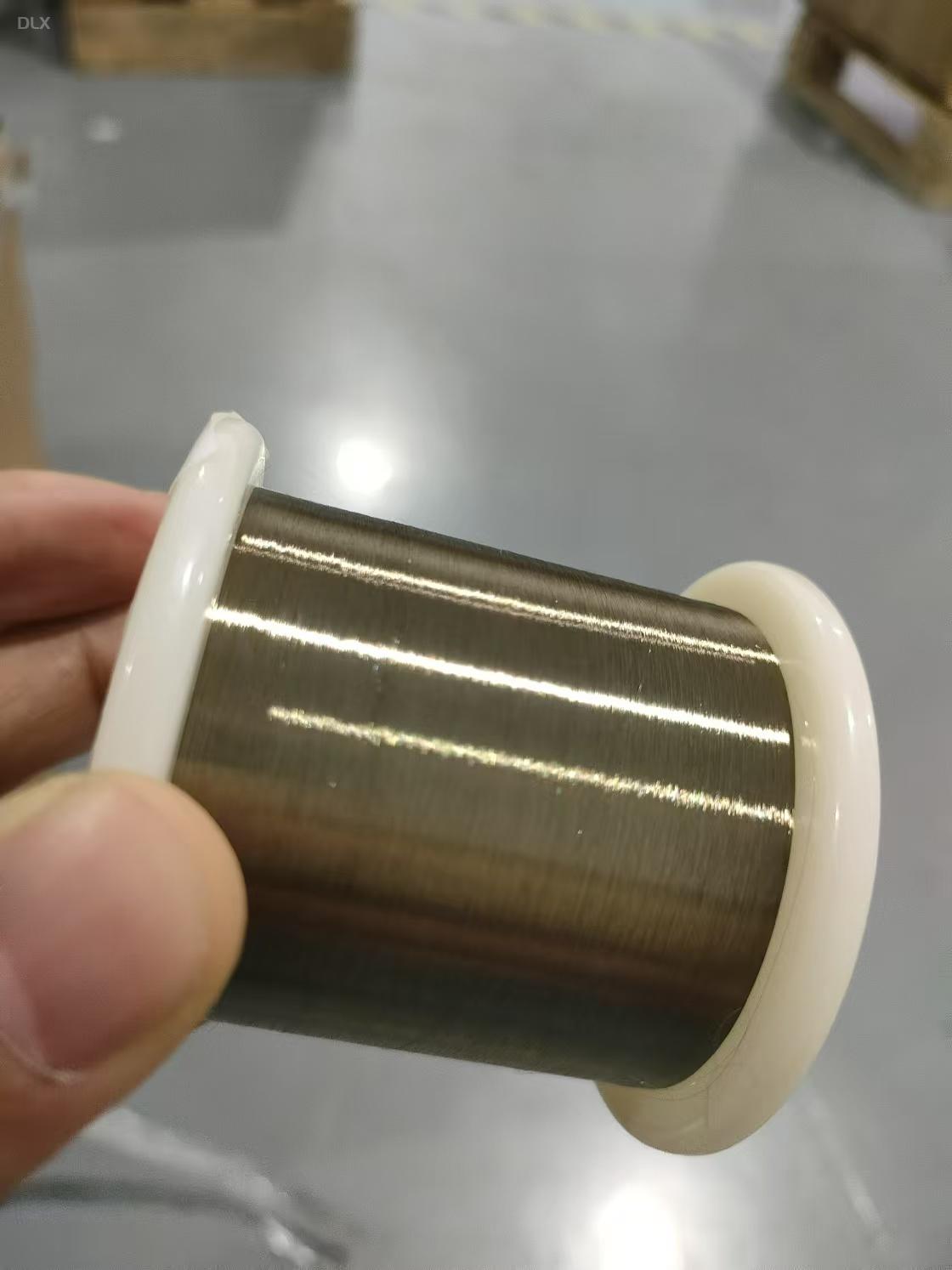
Comparison: DLX Alloy 42 vs. Kanthal Nifethal 42
- Product Details
Comparison: DLX Alloy 42 vs. Kanthal Nifethal 42
Both Alloy 42 and Kanthal Nifethal 42 are Nickel-Iron (Ni-Fe) alloys, known for their low thermal expansion properties. They are commonly used in electronic applications, hermetic sealing, and precision components. However, there are some key differences in performance, manufacturing, and applications.
1️⃣ Chemical Composition
Element | Alloy 42 (%) | Kanthal Nifethal 42 (%) |
---|---|---|
Nickel (Ni) | 41–42 | 42 |
Iron (Fe) | Balance | Balance |
Manganese (Mn) | ≤ 0.8 | ≤ 0.8 |
Silicon (Si) | ≤ 0.3 | ≤ 0.3 |
Carbon (C) | ≤ 0.05 | ≤ 0.05 |
🔹 Key Difference:
Both alloys have nearly identical compositions (~42% Ni, balance Fe).
Kanthal Nifethal 42 is a proprietary version of Alloy 42, optimized for electrical resistance applications.
2️⃣ Physical & Electrical Properties
Property | Alloy 42 | Kanthal Nifethal 42 |
---|---|---|
Resistivity (μΩ·m at 20°C) | 0.62–0.68 | 0.68 |
Coefficient of Thermal Expansion (CTE, 10⁻⁶/K, 20–300°C) | 4.3 – 5.0 | 4.3 – 5.0 |
Density (g/cm³) | 8.12 | 8.12 |
Melting Point (°C) | 1435 | 1435 |
Maximum Operating Temperature (°C) | 450–600 | 450–600 |
🔹 Key Difference:
Kanthal Nifethal 42 has slightly higher resistivity (0.68 μΩ·m), making it more suitable for electrical heating applications.
Thermal expansion (CTE) is the same in both alloys, making them ideal for glass-to-metal seals and electronic packaging.
3️⃣ Key Characteristics & Performance
Property | Alloy 42 | Kanthal Nifethal 42 |
---|---|---|
Low Thermal Expansion | ✅ Excellent | ✅ Excellent |
Electrical Resistance | 🔹 Good | ✅ Better (Higher Resistivity) |
Oxidation Resistance | ✅ Good | ✅ Good |
Corrosion Resistance | ✅ Good | ✅ Good |
Machinability & Formability | ✅ Good | ✅ Good |
🔹 Key Difference:
Kanthal Nifethal 42 is specifically optimized for electrical resistance heating and is slightly better for resistors and heating applications.
4️⃣ Applications
Application | Alloy 42 | Kanthal Nifethal 42 |
---|---|---|
Electronic Packaging (ICs, Semiconductor Leads, Connectors) | ✅ Yes | ✅ Yes |
Glass-to-Metal Sealing (Hermetic Seals, Vacuum Tubes) | ✅ Yes | ✅ Yes |
Resistors & Heating Element s | 🔹 Limited Use | ✅ Optimized |
Precision Instruments (Aerospace, Clocks, Sensors) | ✅ Yes | ✅ Yes |
EMI/RFI Shielding Materials | ✅ Yes | ✅ Yes |
🔹 Key Difference:
Kanthal Nifethal 42 is better for electrical resistance heating applications.
Alloy 42 is more common in semiconductor packaging, glass sealing, and precision instruments.
Final Verdict: Which One is Better?
Category | Alloy 42 | Kanthal Nifethal 42 |
---|---|---|
Low Thermal Expansion | ✅ Yes | ✅ Yes |
Electrical Resistivity | 🔹 Moderate | ✅ Higher |
Heating Applications | 🔹 Limited | ✅ Better Choice |
Glass-to-Metal Sealing | ✅ Excellent | ✅ Excellent |
Cost & Availability | ✅ More Common | 🔹 Less Common |
✔ Choose Alloy 42 if you need:
Low thermal expansion for glass-to-metal sealing
Electronic packaging and precision components
A widely available and well-established material
✔ Choose Kanthal Nifethal 42 if you need:
A low-expansion material optimized for electrical resistance heating
A more stable electrical resistance for resistors and heating elements
A Kanthal-proprietary version of Alloy 42 with improved resistivity
Would you like recommendations for a specific industry or use case? 😊