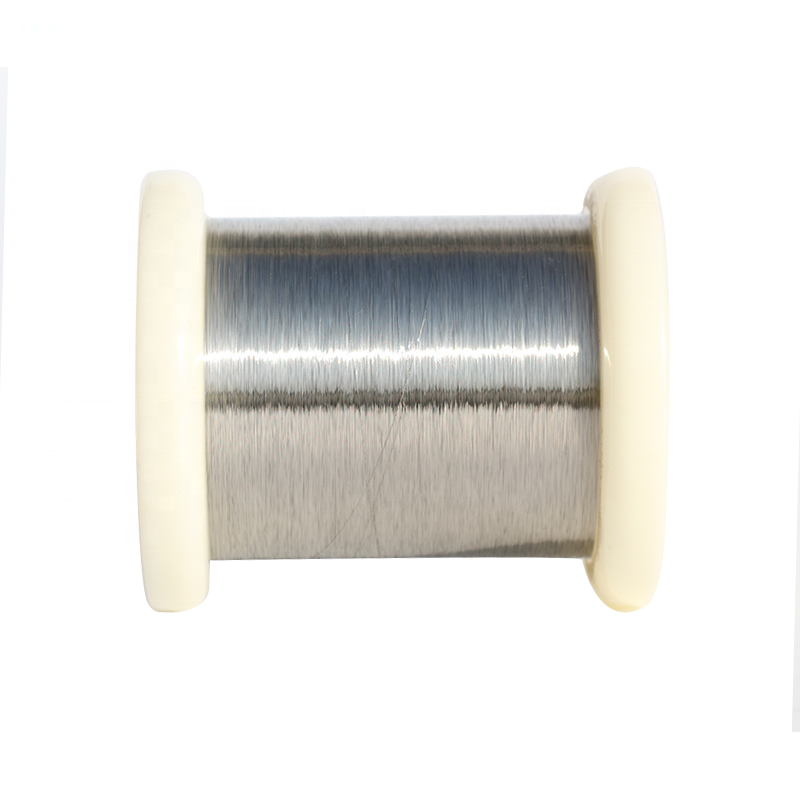
Why is Copper-Nickel (CuNi) More Corrosion-Resistant than Nichrome (NiCr)?
- Product Details
Why is Copper-Nickel ( CuNi ) More Corrosion-Resistant than Nichrome (NiCr)?
Copper-Nickel (CuNi) wire is more corrosion-resistant than Nichrome (NiCr) wire, especially in humid, marine, and chemically aggressive environments. The key reasons for CuNi’s superior corrosion resistance include:
1. CuNi Forms a Stable Protective Oxide Layer
CuNi alloys (e.g., CuNi10, CuNi30, CuNi44) develop a thin, adherent oxide layer of nickel and copper oxides when exposed to air and moisture.
This layer is self-healing and provides long-term protection against corrosion.
The oxide film prevents further oxidation, reducing material degradation.
🔹 Nichrome (NiCr), on the other hand, forms a chromium oxide (Cr₂O₃) layer, which is highly stable at high temperatures but less resistant to saltwater and some chemicals.
2. Superior Resistance to Marine and Chemical Corrosion
CuNi is widely used in marine applications because it resists saltwater corrosion, biofouling, and stress corrosion cracking.
Nickel in CuNi alloys enhances resistance to acidic and alkaline environments.
CuNi resists sulfide stress cracking (SSC) and chloride-induced corrosion, making it ideal for seawater piping, ship hulls, and underwater cables.
🔹 Nichrome is more susceptible to chloride-induced pitting and stress corrosion cracking in seawater or acidic environments.
3. CuNi is Less Brittle in Corrosive Environments
CuNi remains ductile and flexible, even after prolonged exposure to moisture, chemicals, and mechanical stress.
Nichrome can become brittle over time, especially when exposed to oxidizing and sulfur-containing environments.
🔹 This makes CuNi more suitable for long-term outdoor applications, such as heating cables and marine electrical systems.
4. CuNi Performs Better in Low-Temperature & Humid Conditions
CuNi does not degrade as quickly in high-humidity or low-temperature conditions.
It is resistant to moisture-related oxidation.
In contrast, Nichrome may suffer from oxidation in humid environments, leading to performance degradation.
🔹 This is why CuNi is preferred for
✔️ Floor heating cables
✔️ Marine resistance wires
✔️ Thermocouple extension cables
5. CuNi Has Better Sulfur and Hydrogen Sulfide (H₂S) Resistance
CuNi is resistant to sulfur-containing gases and hydrogen sulfide (H₂S), commonly found in industrial environments, oil refineries, and marine conditions.
Nichrome is susceptible to sulfur attack, leading to embrittlement at high temperatures.
🔹 This makes CuNi a better choice for industrial and marine heating applications.
Comparison of Corrosion Resistance: CuNi vs. Nichrome
Property | CuNi (Copper-Nickel) | Nichrome (NiCr) |
---|---|---|
Marine Corrosion Resistance | ✅ Excellent | ⚠️ Moderate (can corrode in seawater) |
Oxidation Resistance | ✅ Good (protective Cu-Ni oxide layer) | ✅ Very High (Cr₂O₃ layer) |
Resistance to Chlorides & Salts | ✅ Excellent | ⚠️ Moderate (can suffer pitting in saltwater) |
Moisture Resistance | ✅ Excellent | ⚠️ Can oxidize over time in humid conditions |
Sulfur & H₂S Resistance | ✅ High | ❌ Poor (suffers from sulfur embrittlement) |
Ductility & Mechanical Strength Over Time | ✅ Remains ductile | ⚠️ Can become brittle in harsh conditions |
Best Applications | Marine, heating cables, thermocouples, industrial wiring | High-temperature heating elements, furnaces |
Summary: Why is CuNi More Corrosion-Resistant than Nichrome?
✅ Forms a stable, self-healing oxide layer that protects against corrosion
✅ Superior resistance to saltwater, chlorides, and acids
✅ Resistant to sulfur and H₂S attack, preventing embrittlement
✅ Remains ductile and strong in humid or corrosive conditions
✅ Ideal for marine, industrial, and heating applications